What Is Smart Manufacturing, and How Will It Revolutionize Your Industry?
Industry 4.0 is here, whether you’re ready or not. Industry 4.0 is defined by modern automation and data exchange trends in manufacturing technologies that continue to fuse physical, digital and biological capabilities.
The term Industry 4.0 is best defined as “a fusion of technologies that is blurring the lines between the physical, digital, and biological spheres, collectively referred to as cyber-physical systems.” – Klaus Schwab
Thanks to ever-advancing digital technologies like the Internet of Things, 5g wireless innovations, 3D printing, augmented reality and beyond, modern manufacturing environments are changing at a rapid pace, and there’s no slowdown on the horizon. New tools, techniques, and optimized production processes will continue empowering savvy industrial organizations to drive both top-line and bottom-line growth through exciting new digital initiatives.
A fusion of technologies that is blurring the lines between the physical, digital, and biological spheres, collectively referred to as cyber-physical systems. – Klaus Schwab, Founder and Executive Chairman, World Economic Forum, 2016
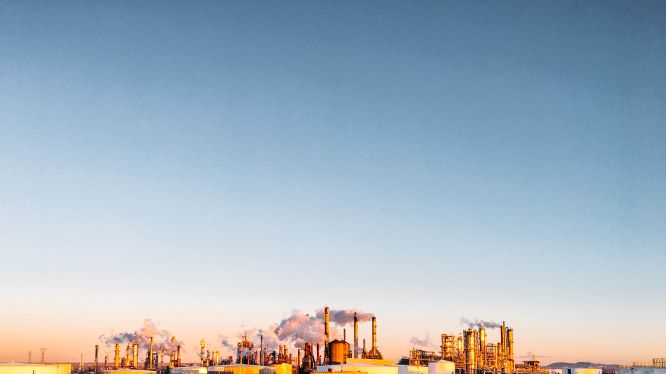
But when considering what digital transformation strategy you should pursue, it’s not always clear what’s going to have the biggest impact on your organization both in the long- and short-term. For large manufacturers, competing with newer, more nimble companies by adopting impactful new technology is a daunting challenge with difficult to understand implications. To better prepare your organization for the inevitable changes, let’s explore what makes “smart manufacturing” smart, how the internet of things is bringing about the 4th industrial revolution, and what manufacturers need to know to take advantage of it.
To begin, make sure you’re caught up with the latest definitions.
What is Smart Manufacturing?
“Smart manufacturing” is broadly defined as leveraging advanced technology to automate data collection and processing to make much more informed production decisions on a day-to-day basis.
While this definition barely touches on the full breadth of possibilities brought on by smart manufacturing, it still demonstrates – from a high level – what smart manufacturing is all about. However, when you examine many examples of smart manufacturing applications and benefits, you’ll find that the most prominent factor driving these technological advancements is the Internet of Things – otherwise known as IoT.
What is the Internet of Things?
The internet of things (IoT) is a conceptual term that describes the connection of physical objects to the internet. The easiest way to think about IoT is as a huge network of connected objects and people. Objects connect to other objects (the global number of connected devices is now in the billions), and people connect to objects. These connections then allow the objects and people to send data back and forth to each other. Armed with new information, people make decisions about the connected objects, and with A.I., the objects can also automatically make decisions about other objects – all in real-time.
Whether you realize it or not, we’re all likely contributing to the internet of things. Some of the most familiar examples of how IoT technology is already integrated into everyday life include:
- Smart home devices – A 2017 research reported estimated that 79% of American homes already own at least one smart device. For example, wifi-enabled washing machines and dryers can inform owners of their status at any given moment. This enables the owner to make laundry-related decisions from afar, sending programming instructions to the machines to fluff, start a load, or whatever the owner thinks is the best course of action based on the data they received from the sensors in the laundry machine. There are many home devices with similar (and more advanced) functionalities, from lights to cooking appliances to thermostats.
- Fitness Wearables – These have been around for decades, but internet connectability has transformed the entire industry surrounding fitness tracking devices in terms of how that data is used. Sure, people can still use these wearables for their original intent – to monitor their health stats and track daily activity levels. Now, however, that user health data is often used by health insurance companies to make key business decisions: determine premiums, incentivize individuals who have high activity, and in a broader sense, help to decrease payouts for health-related issues. It can also be used to improve data capture in health studies, like the collaboration between Stanford and Apple to study heart health.
But, the above consumer applications don’t even scratch the surface on how IoT is currently being leveraged across businesses globally, let alone how it will be leveraged next year, or in 10 years. And, as you will see, these applications are well underway in the industrial sector.
Industrial Internet of Things (IIOT)
The Industrial Internet of Things (IIoT) is the concept of IoT as applied mainly to manufacturing and applications in related industries like logistics, oil and gas, transportation, energy/utilities, and other industrial sectors.
IIoT allows manufacturers to leverage wired and wireless technologies with many impressive results. For example, by enabling the real-time flow of data and providing manufacturers with the ability to remotely monitor and manage various processes in their warehouses and factories, IoT greatly improves the efficiency of daily operations.
At the same time, IoT also helps manufacturers reduce waste, automatically share production data with stakeholders, and change plans in real time whenever necessary. As far as many industry leaders are concerned, these are the key benefits of having advanced IoT in manufacturing facilities – and that’s not expected to change any time soon. In fact, it’s been estimated that industrial IoT could well be one of the biggest drivers of productivity and growth throughout the next decade, adding as much as $14.2 trillion to the global economy by 2030.
IIOT & Smart Manufacturing
According to Markets and Markets research, the smart manufacturing market is projected to be valued at $205.42 Billion by 2022, while another prominent report projects the IIoT market reaching $933.62 billion by 2025. With IoT tech applications primarily driving this rapid growth, other factors include the increased adoption of industrial robots, heightened demand for smart automation, and a much stricter emphasis on regulatory compliance.
North America is a key market region for both IIoT and smart manufacturing growth because it’s home to some of the world’s largest multinational manufacturing companies. These industry-leading internationals are investing significant amounts of their R&D budgets to uncover even more innovative IoT possibilities that help move their businesses forward, which is one of the most crucial factors driving the growth of this market throughout North America.
Potential Benefits of IIoT
IIot implementation opportunities are seemingly infinite. From production processes to distribution logistical data, to initiatives in HR, marketing and beyond, the limitless potential of a scalable IIoT strategy can provide the confidence you and your stakeholders need to remain poised for, and ever-capable of, competitive differentiation in an era defined by how well traditional companies take advantage of the latest technological advancements.
For manufacturers, the immediate benefits of IoT adoption could include:
- Improving operational efficiency
- Increasing productivity
- Creating new business opportunities
- Reducing downtime
- Maximizing asset utilization
- Lessening asset lifecycle costs
- Enhancing worker safety
- Strengthening product innovation processes
- A better understanding of customer demand
So as a manufacturer, how do you prepare your organization for this transformative technology and reap all the benefits you can?
How Manufacturers are Getting Smarter
According to 2016 data compiled by Visual Capitalist, only 30% of industrial organizations said they were either piloting or implementing IIoT projects currently, while 70% indicated they were in consideration, early discussions or planning phases. In fact, early adopters of IIoT technologies like the companies highlighted below are seeing big returns that will continue to increase efficiency and promote cost savings for years (maybe decades!) to come.
GE Builds Smart Trains
As a pioneer in IIoT, (they actually coined the phrase “industrial Internet” which eventually became IIoT) GE’s latest locomotive engine models are each equipped with 30+ sensors that constantly transmit data on oil pressure, manifold air temperature and other mechanical/functional engine data. The data is relayed to GE Transportation’s Global Performance and Optimization Center, where it is compiled and then analyzed via a single dashboard to plan out maintenance and repair initiatives (including pre-emptively securing needed parts) and improve the overall efficiency of each engine in service.
Results
GE currently has over 17,000 smart trains operating across 23 countries for which they’ve reduced repair time windows from 3 days to 3 hours, since implementing the new smart trains. They have also reduced emissions by 70% per train.
Hershey Twizzlers Production Efficiency
Hershey recognized some potential savings opportunities within their candy production processes, specifically with one of their classic brands – Twizzlers. In an attempt to reduce the amount of product and materials waste, Hershey installed 22 sensors to assess the temperature of cooking vats and ultimately quantify the factors and conditions that make their Twizzlers either too long, too short, or just right.
Results
Coupled with machine learning and data analytics, Hershey was able to make sense of 60 million data points collected via automation to reduce the variety in candy size to ensure each piece is no longer than necessary, generating huge savings. By cutting down on excess candy produced, Hershey has been able to save about $500,000 per 14,000-gallon holding tank for every 1% change in actual Twizzler size. With multiple holding tanks, the expected savings should exceed $1 million annually for this initiative alone. Hershey is currently implementing similar initiatives to their vast line of chocolate-based products, and since chocolate ingredients are much more expensive than the basic flour and sugar combination in Twizzlers, Hershey expects an even greater production impact and bigger savings down the road.
ThyssenKrupp – Elevator Maintenance
ThyssenKrupp is a German-owned multinational conglomerate with deep roots in industrial engineering and steel production (one of the world’s largest). Also a prominent manufacturer of elevators, Thyssenkrupp installed thousands of sensors across all of their elevators around the world. Each sensor transmits specific data about each elevator in service, including motor temperature, shaft alignment, cab speed, door functionality, error codes, and more. The entire system is connected to the cloud where unique algorithms analyze the incoming data for patterns and compute the components’ remaining lifetime and the overall operational efficiency of each piece of equipment.
The data is then viewable via a single dashboard that not only compiles it into a single location but also automatically visualizes the data for quick interpretation. The entire system informs a network of 24,000 service engineers about specifics related to maintenance of the elevators. Technicians are then able to be more proactive with their maintenance and repair scheduling, including intervening before elevators breakdown, and scheduling service when there will be minimal disruption and when downtimes won’t impact the building workers. Technicians can also determine where and how elevators are failing based on usage specifics.
Results
With this system in place, ThyssenKrupp has been able to greatly streamline their service to elevators, freeing up over 95 million hours in total labor time for engineers while also substantially eliminating elevator downtime during heavy usage hours. The initiative has been so successful that ThyssenKrupp has recently introduced a similar system for their escalators.
How to Leverage IoT Trends in Manufacturing
From immediate returns to laying the foundation for future AI-enabled advantages, IIoT gives industrial organizations the competitive advantage needed to remain at the front of the pack. Fortunately, there are countless opportunities to leverage the proliferation of smart technologies to your advantage that you might not have even realized yet.
Still, due to the complexities and large-scale changes needed to both understand and then implement an effective digital transformation, many organizations struggle with finding a solution to effectively manage all of the data they are generating, or hope to in the future. There is no “easy button” here, but there are certain steps (ranging from simple to complex) to position your company to better leverage IIoT technologies in the near future.
Smart Steps to IIOT Adoption
Becoming a smart manufacturer is heavily predicated on your company’s ability to adopt scalable digital technologies, many of which are deeply rooted in IoT foundations. In many cases, there are certainly some large technological systems and infrastructure updates that will need to be made in advance of being able to optimize the efficiency of your assets and the people that interact with them.
You’ll, of course, need to first ensure that you have strong internet connectivity throughout your manufacturing facility and that the network is capable of handling the increased workload and data transfers you expect in the future. But just because an object is connected to the internet, doesn’t mean it’s going to immediately start sending you concisely worded emails about itself, complete with data tables that highlight gaps in your product efficiency. This type of automated data gathering is within reach if your systems are set up to operate appropriately.
Below are some high-level steps and considerations as you begin to develop your strategy to leverage IoT effectively, and with future scalability in mind.
Connect & Collect – Install Sensors & Upgrade Equipment
Laying the technological groundwork for streamlining your manufacturing production environment is all about first determining what data you want to capture for analysis, and then installing the necessary hardware to begin collecting that data. Wifi-enabled smart sensors make the collection possible, whether it’s an off-the-shelf product or a custom built tool to meet your unique needs.
When planning out the sensor installation, make sure to get input from your end users, be they engineers, technicians or shop floor managers. They will help determine what you will need each sensor to do/provide, which often varies for each set of users (if there are multiple). Some questions your implementation team should be asking are:
- Do you need to visually monitor an out-of-view component? Then you’ll likely need to use cameras, a “digital twin,” or both.
- Will you need alerts? Do they need to be real-time or based on aggregate data? Defining the triggers, the actual alerts, and protocols to handle them add a layer of strategic complexity to seemingly simple features.
- Do you need a specific type of connectivity with the sensors (Wi-Fi, Bluetooth, Zigbee, etc.)?
- What are you measuring – temperature, velocity, pressure, valve open/closed status, proximity and spacing, GPS data, etc.?
Determining the right hardware to install is no easy process, so make sure you run through all of the potential possibilities and needs with all of the people using the systems. Prioritization of initiatives is key with any digital transformation because, while the possibilities are endless, your source of funding is finite.
Store the Data – Cloud Computing
Leveraging cloud computing is the ideal way to incorporate scalable digital technologies that help manufacturers store, disseminate, and analyze data that comes from your things. You could consider it a critical first step in your digital transformation. You can’t use the data until you have somewhere to house it, and later access it.
The days of having all your organizational data stored and computed on-premises is quickly becoming a thing of the past. Businesses are able to avoid many of the complexities that come with IoT adoption because cloud computing and storage environments are already set up for these kinds of advanced computation and connectivity. Advancements in cloud capabilities are growing much faster than most internal IT teams could ever dream of keeping pace with. Cloud computing and cloud storage have become a more cost-effective and reliable solution, encouraging more and more manufacturers to migrate to the cloud from on-prem.
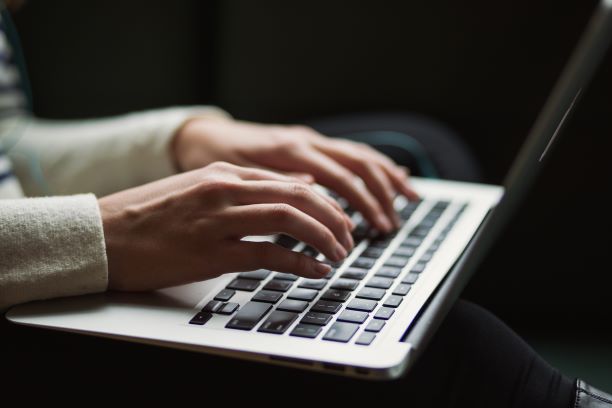
Data protection, back-up and recovery, real-time analytics and computing, ease of maintenance, etc. – the benefits of cloud computing are plentiful. With an expanding market, increasing competition, and companies unbundling previously packaged services, the overall cost of cloud storage continues to drop, becoming equal to or more cost-effective than internal system storage.
According to research conducted by Morgan Stanley, the top 5 challenges that concern today’s automation executives include:
- Cybersecurity
- Lack of standardization
- Legacy-installed base
- Significant upfront investments
- Lack of skilled workers
A solid cloud strategy makes most (if not all) of these challenges much easier to tackle, as specialized technology and tools are available across a variety of cloud storage vendors.
Compile & Combine the Data
The last thing anyone wants is another platform to log into, let alone one for each data sensor. But before you start logging in and reaping the benefits of automation, the data needs to be compiled and combined into a single data repository. This is where savvy software engineers technical leads become a key part of your digital transformation: they help compile your various and vastly differing datasets for computation, all accessible via an easy-to-use platform for IT and non-IT personnel alike.
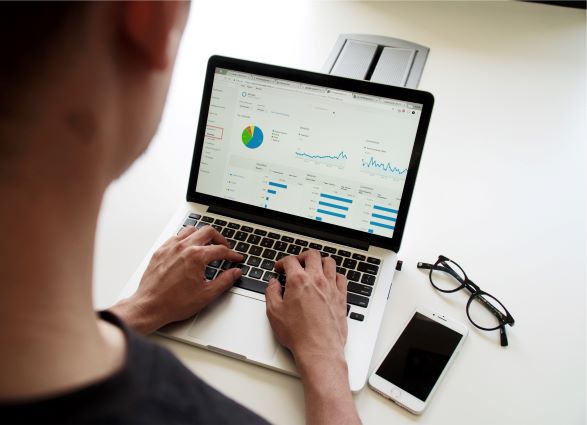
From a maintenance perspective, unique algorithms can be designed to help auto-identify any issues and predict when issues might occur. As specific issues or pre-emptive warnings arise, the system can then send notifications to your team in whatever format is preferred and allow them to either take action from there (sending commands back to the machine to adjust) or simply schedule physical maintenance tasks at specific times, depending on the severity of the issue and systems.
Before taking any action, however, your users need to be able to understand the compiled data.
Convey The Data
Once the data is collected, compiled and consolidated, it then needs to be prepped for the human eye to be able to make sense of it. This is when data visualization experts and UX designers alike help to craft user-friendly dashboards that represent data in a way that allows your everyday users to:
- quickly and easily spot issues or anomalies with the data
- determine sets of common next steps or commands that can be instantaneously implemented
Secure The Data
Connecting elements of your manufacturing production to the internet certainly brings about new security challenges for your IT team. In fact, in a recent survey, 39% of executives respondents indicated that privacy and security are the most significant barriers to IoT investment.
Within an unsecured or loosely secured system, a malicious hacker or negligent user could wreak havoc on your production facility or processes with potentially devastating consequences.
Your automation and smart manufacturing strategy should always include layers of security intertwined throughout. On this front, you won’t go wrong borrowing from the playbook of the United Kingdom’s National Cyber Security Centre (NCSC). They follow the classic idiom, “hope for the best, but prepare for the worst.” To effectively prepare for the worst when designing a system or network:
- Assume that every step in your system will fail catastrophically. You’ll be working with highly complex systems built by arguably the most error-prone and complex systems in the world (humans).
- Design your network to reduce the reach of each individual catastrophic failure.
These steps should be reinforced by setting standards of security for any vendor you work with, creating defense in depth. Some factors to consider when creating your own standards are:
- The security of the development lifecycle for any vendors
- The vulnerabilities created or reduced by product design (a classic example of this is immutability of cloud storage buckets)
- The efficiency with which vulnerabilities and breaches can be patched
The last nugget of wisdom provided by Ian Levy, Technical Director of the NCSC, is put too eloquently to summarize:
If your passwords are all system defaults, it doesn’t matter whose kit you use, you’re stuffed. If you don’t monitor the system for changes, you’re stuffed. If you don’t manage privilege properly, you’re stuffed. If you allow a third party to run your network and have no in-house capability to audit what they’re doing, you’re stuffed.
Luckily, cloud storage providers recognize these as non-negotiables and can help with much of the heavy lifting needed to secure the data. But, every manufacturer should do their due diligence to ensure access is restricted to these critical systems, from hardware to software and everything in between. There’s no denying that you will have a lot of new potential points of failure to roll up under your blanket of security.
Analyze the Data
If the data is flowing in and is easily accessible and understood by your human stakeholders, then data analysis processes should be relatively simple, as well. Analyzing the data starts with determining what analysis automation aspects you want the machines to carry-out versus where human analysis and intervention is crucial.
For humans, how the data is conveyed plays a key role in their ability to analyze and take the necessary next steps to remedy anything, keep things running smoothly, and unlock efficiencies. For automation systems and robots, they’re always going to be following the human lead. They are only going to take the actions they are programmed to do based on the data. Intelligent programmers are therefore essential in setting up any automated aspects where machines make decisions to change something in your facility or organization.
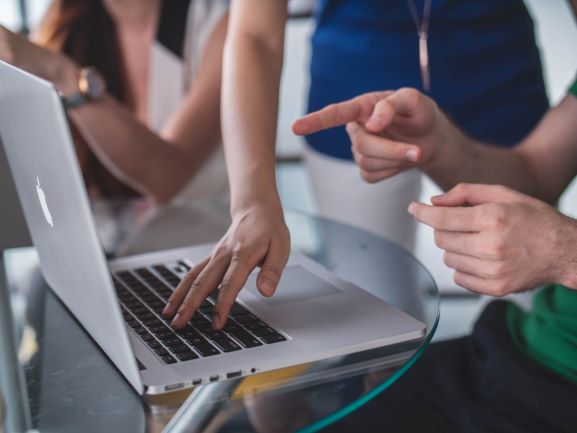
Humanized Digital Transformations
In spite of the nonstop advancements being made with industrial IoT applications, it’s still human beings who are ultimately tasked with coming up with the right strategies and putting these technologies to use. That means you’ll need to stay on top of emerging trends and opportunities in the field if you want your strategies to remain relevant, while also utilizing your IIoT solutions to their full potential.
Of course, it helps to have an industry-leading digital agency and software development company on your side to help steer you down the right path, keep you up to date with the latest digital transformation trends, and utilize your resources in the most efficient way possible.
Contact us today if you’re ready to take your industrial IoT applications to a new level of smart.